Winner | National Satellite Test Facility, Harwell Science & Innovation Campus
National Satellite Test Facility, Harwell Science & Innovation Campus
Words by Arcadis
In 2016, the Arcadis architectural and landscape team were commissioned to design the National Satellite Test Facility (NSTF), located on the Harwell Science and Innovation Campus. The brief was to create a world-class cleanroom test facility, comprising six enormous chambers to replicate the extreme conditions a satellite encounters in deep space, from launch to orbit. The Diamond Light Source, the UK’s national synchrotron light source science facility, also located at Harwell Science and Innovation Campus, is so sensitive to movement that it must be isolated from vibrations from the A34 (more than a kilometer away), just to prevent heavy goods vehicles from ruining its delicate experiments. With the NSTF site just 100 metres from the accelerator, the decision was made to construct as much of the building as possible offsite.
The main structure was conceived as a hybrid of steel and cross laminated timber (CLT). The benefits were twofold; firstly, the timber frame was more carbon-friendly than traditional concrete slabs, and secondly, its lightness meant that there was a reduction in requirements for the foundation depth. This saved on concrete pour, environmental impact, and crucially removed the need for disruptive and vibration heavy digging or piling which could have disturbed nearby experiments on campus.
Each CLT panel and piece of steel was designed and coordinated in a 3D BIM environment across the whole design team, inclusive of the specialist experimental equipment manufacturers and supply chain, to ensure that they would come to site ready to slot into place and accept the buildings complex mechanical and ventilation requirements, without the need to so much as drill a hole post-delivery. Even the basement of the building was created via a system of offsite manufacture. Huge tunnel sections similar to those used in the development of Crossrail were driven vertically into the ground to create a preformed basement structure. The sections were delivered to site via lorry and bolted together before being waterproofed to create a mechanical pit for the building’s vibration testing chamber.
Modularising the frame and floor slabs meant road movements could be minimised for the main frame, but this thought process also bled over into the design of the envelope. Heavily insulated, preformed, 240 millimetre aluminium panels with airtight gaskets span directly across the buildings primary frame members.
Whilst panellisation and offsite manufacture allowed us to minimise movement to and from the site, there were some unique deliveries that were required. Transporting the buildings thermal vacuum chamber (TVAC) to site required the remodeling of Portsmouth Docks in one of the largest single road movements in British history, and closure of the motorway to allow the sixteen-by-eightmetre, 98-tonne chamber to be delivered to Harwell. The chamber now forms part of the actual fabric of one of the main cleanroom walls.
Technically, this posed additional challenges, the TVAC itself simulates the cold of space and heat of the sun on a satellite, but these intense changes also affect the outer skin of the structure, and as a result, its interface with the building. Partition junctions were specially crafted to not only deal with the curved eight-metre radius of the chamber itself, but also to flex and move during its expansion and contraction as huge quantities of liquid nitrogen coursed through its walls.
The vibration testing chamber consists of two shakers which are individually damped with over 100-tonne concrete counterweights, seated on hydraulic springs sitting in a basement below. The noise created by these shakers is in excess of a jet plane at takeoff, and the vibrational forces are large enough to literally tear a building apart. As such the room is structurally and acoustically isolated to an extremely high degree. The pressure cascade is an incredibly important feature of the building, and the reason this facility is one of only a few globally that is able to keep satellites ‘clean’ through multiple tests without the need to repack and clean down.
To create this functionality, we worked closely with RAL Space’s scientists to create a whole new testing process, where satellites could be unpacked at a singleentry point at the start of their journey and then remain in a clean environment whilst they navigated the full gamut of testing, like a factory production line. The anechoic is used to provide a pristine environment to test a satellite’s communication abilities and ensure that when it is hundreds of thousands of miles from home it can still relay information back to Earth. Of course, to send such a signal, huge quantities of energy are needed. This energy in turn then must be absorbed, the anechoic chambers foam cones acting as sponges to this excess output. However, due to the power generated, they can occasionally be heated to such a point they spontaneously combust. To prevent this, the chamber had to be designed with a hypoxic oxygen depletion system.
The hypoxic system dilutes the oxygen in the air, effectively thinning it to create conditions akin to that of scaling Everest. This thinning of the air helps to quell fires from starting by starving them of oxygen. Unfortunately, scientists also require oxygen to work, hence the system having to be delicately balanced, and the room carefully detailed to be sealed to prevent suffocating those working inside. This test also needed to prevent signals and interference getting in. Hundreds of copper reflector plates help to drown out the outside world, with each placed millimeter perfect, with the exact correct length of fitting screw to prevent an electrical bridge that would render the chamber useless. This was backed by an earth mat the size of a swimming pool that had to be concealed underground to the perimeter of the site.
Dovetailing these complex requirements was a huge technical challenge, which NSTF managed to address via smart detailing solutions and commitment from the specialist teams that were contracted to construct the building. They worked in unison to provide a facility the UK space industry can rightfully be proud of and that can evolve over the next age of space travel and exploration.
Entry boards
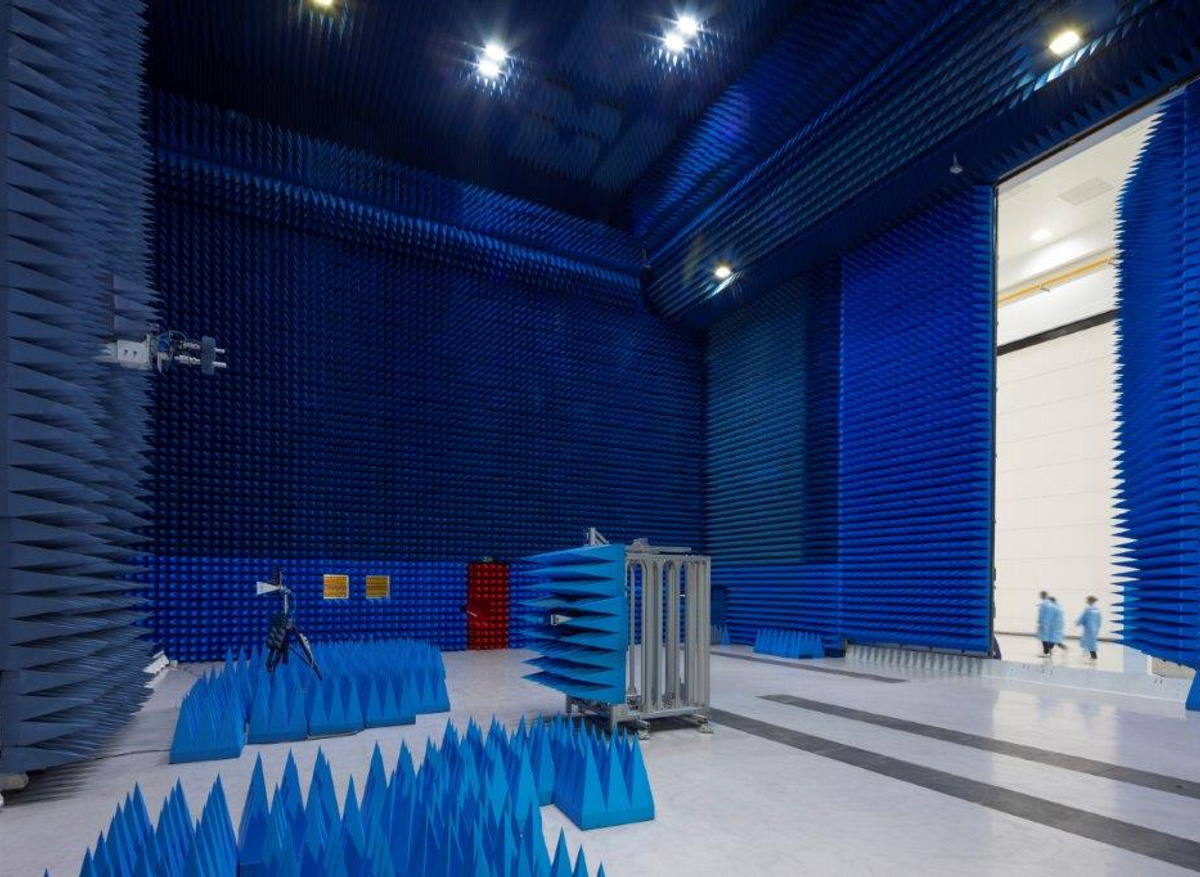
-
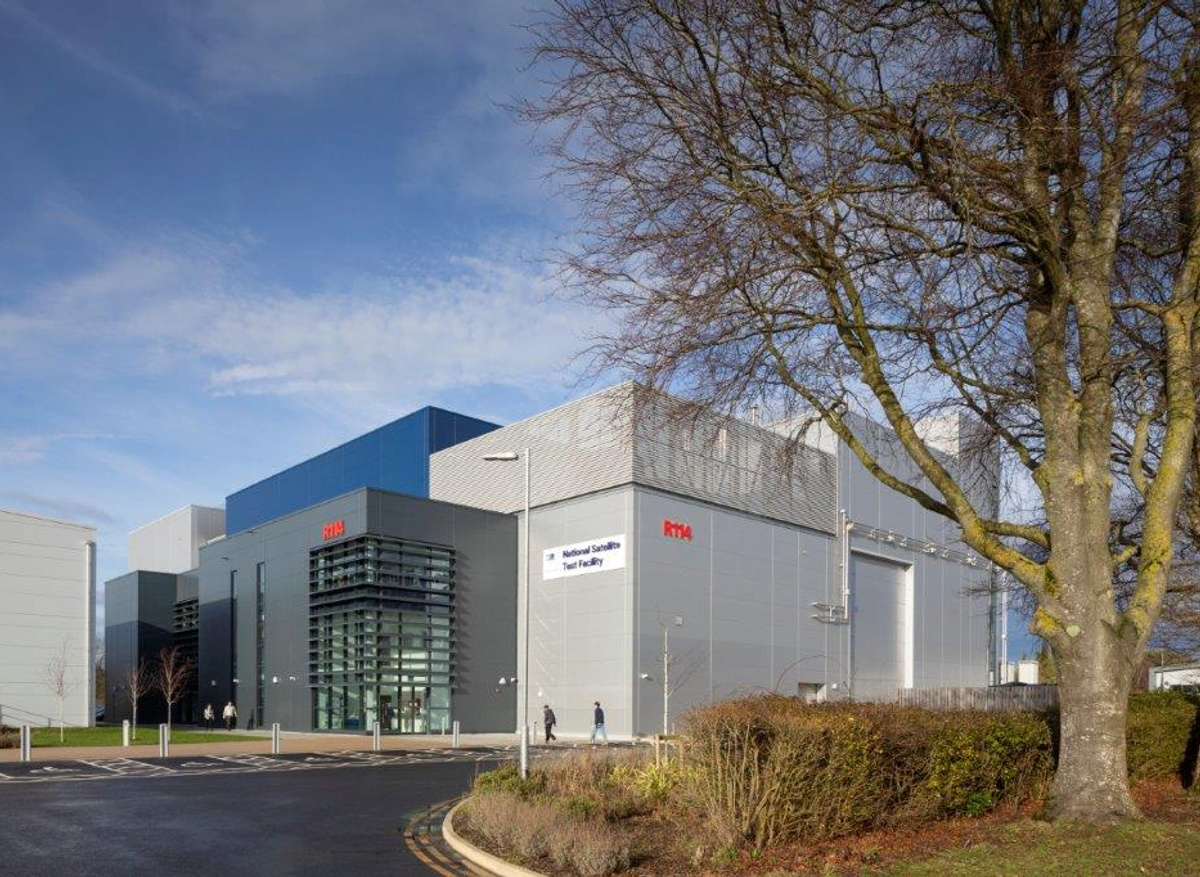
-
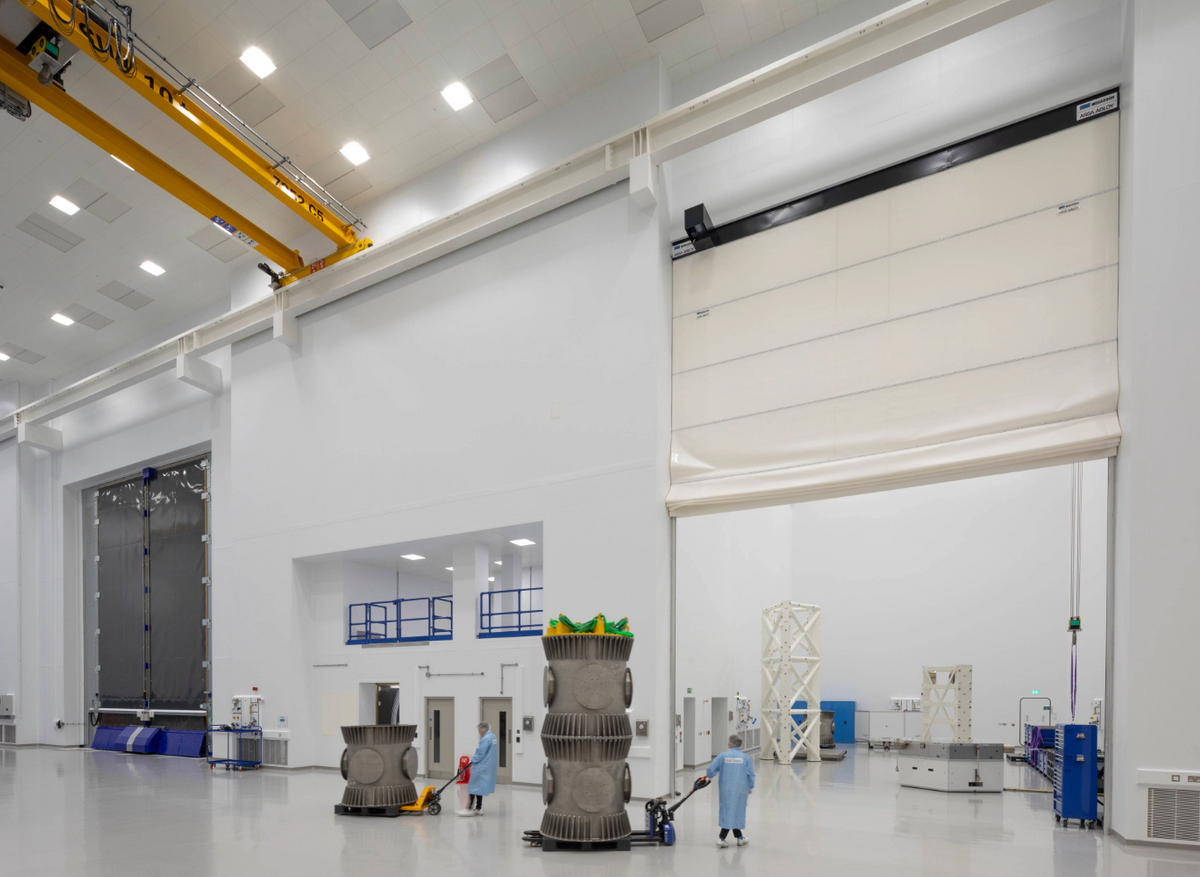
-
Judges' comments
This project involved the design and construction of a world-class cleanroom test facility, comprising six enormous chambers to replicate the extreme conditions a satellite will encounter in deep space, from launch to orbit. Almost every detail in the project required a comprehensive level of innovation to satisfy the unique requirements of each space; it was impressive how this project was designed and managed. The Judges were impressed by the high standards of technical detailing and almost unfathomable construction tolerances of 1.5 nanometres: the amount your fingernail has grown whilst reading out this sentence. A worthy winner of the large-to-mega category.