Words by Stuart Davidson FCIAT, Stuart Davidson Architecture
Our clients appointed us to create a new STEM teaching and learning hub as part of a larger re-development project for their campus.
Located to the east of the anterior A7 trunk road forming a long slither of flat land with a large steep bank to the east, the chosen location was pre-formed as a tarmac area formerly used for external learning and bin storage. The benefit of this allowed us to simplify the initial site works. The overall aim was to utilise the Hub to support the campus regeneration as a sustainability and development hub for the overall college.
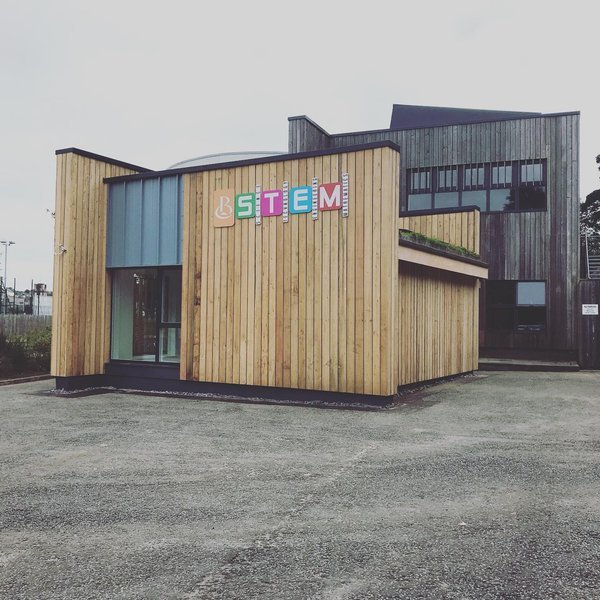
The existing college building and its narrow site controlled the available space and site location with only two available sites an initial feasibility carried out by ourselves clarified that only one site was suitable for use, though still restricted by a large bank to the east restricting solar gains though using the benefit of the existing structure to the north to reduce chilling of the building.
The brief for the building was to ensure full connectivity with the existing college, though be able to be used as a separate entity for training and seminar use out of college hours. The structure was also to be designed to allow for continual monitoring and testing of the structure including fabric and airtightness over the lifetime of the building.
Our aim initially was to create a building which used all of the ethos of Passivhaus at a simplified cost effective level which should ideally not require any form of heating, though after initial assessment due to the restricted orientation of the build we designed the addition of a single 200W electric heating panel, which gains power from the PV solar panels located on the roof.
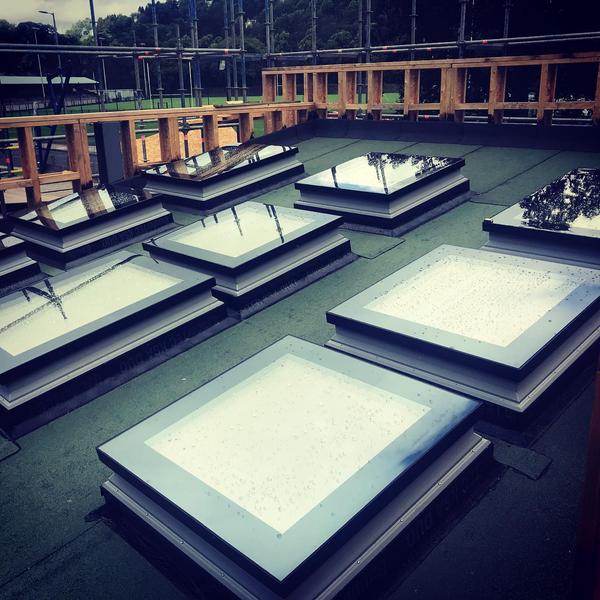
The location was chosen for its simplistic initial build and suitability for site traffic ensuring that initial costs and ongoing site manoeuvrability was controlled. The site levels allowed minimal excavation prior to forming the new passive slab with tarmac cut back to allow for the formation and re-dressing afterwards. The single skin kit formation was initially designed to be factory casements, though due to extended lead times and limited access for cranes due to the location, the structure was site built with additional inspections to ensure structural and performance compliance by ourselves.
Though the site was fully accessible the working space was restrictive so controlled trades working areas were paramount to make sure that each dovetailed into each other such as the interaction between green roof and solar installations or the sealing of services with insulation and roofing.
The building’s prime function is a teaching/learning space as well as a “testable structure” as the floor level is raised some 400mm from FGL the linkage to the main college was paramount to ensure that full accessibility is obtained at all times, the addition of a link lobby allowed this to be formed whilst also providing an environment lock between the two buildings.
As noted the building has to be testable at all times, this was factored in from the design stage with blower door testing locations designed in, additional doors formed to allow testing of separate elements of the structure, removable sections of internal finishes such as unscrewable skirtings, exposed wall/roof junctions to inspect the performance of airtight membranes between differing materials and structural items.
Future proofing maintenance to suit our clients needs were designed into the structure. Service voids were formed internally to all walls and ceilings to allow retro fit services without damaging the fabric, pre-determined and sealed ducts installed for any external monitoring and full connectivity with a similar STEM facility in Dumfries pre-installed. It was found that previously “fall assists” on the existing building had not been used so the addition of raised parapets to the new building and cherry picker accessibility was designed into future maintenance plans to ensure safety is paramount.
The building though not ideally located for solar gains were designed to accommodate for this, a simplistic mono pitch roof with parapet wall with additional high performance rooflights providing solar gains, with automatic thermostatic controls to ensure no overheating.
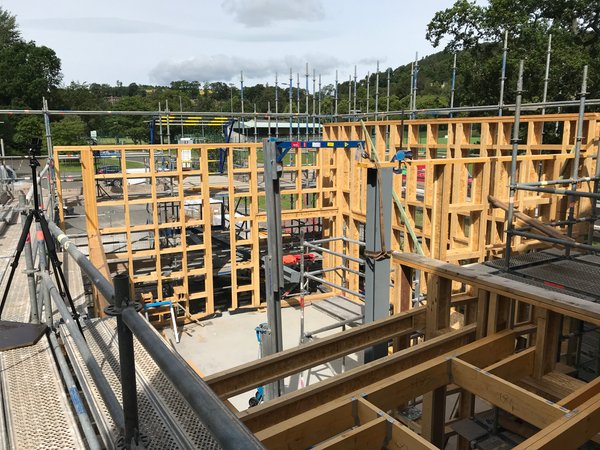
Timber louvres have been provided to westerly facing windows due to known overheating issues to the existing building and southerly mounted PV solar panels installed to the roof provide an over allowance for pre-determined energy use within the building, this coupled with internal monitoring infrastructure allows the clients to assess the usage and feed back to the main building.
The structure overall incorporates a passive concrete slab used as a heat sink, with walls and roof formed from a single skin oversized I beam structure insulated with pavatherm insulation within and outside the kit. It was sealed using proclima variable airtightness membrane and clad with scotlarch cladding to match the existing building. The roof is finally finished with a low maintenance wildflower blanket forming significant thermal mass to retain all embodied energy within the building.
The building as a whole as been tested to an “as built” measured air permeability of 1.24m3/(h.m2) which almost exactly matches the design performance target. This was provided by the marrying of the mixture of overlapping insulation methods, specific taping both internally and externally with guided “toolbox talks” by ourselves on site, high performance windows and doors to remove any points of weakness.
At design stage all details were focused to ensure that maximum performance was maintained with simplified detailing at junctions to make on site construction simpler. A single MVHR unit was predesigned to suit the performance of the building, again to aid teaching this is fully exposed including ductwork maintaining air quality and movement. This is also powered by the solar panel supply with monitoring software assessing usage.