Words by Gale & Snowden Architects Ltd
Starting as a research project in 2012, Gale & Snowden helped to obtain funding from the Technology Strategy Board (TSB) to assess the impact of future climate on a leisure centre proposed across various locations in the city of Exeter.
The design team were to provide a low-energy Passivhaus design that incorporated healthy building principles, and Gale & Snowden's responsibilities included computer modelling and design for future climate change adaptation as well as 'architects for the envelope of the building'.
Gale & Snowden Architects joined Space & Place Architects (as lead designer) and Arup (as engineers), which integrated a design team for architecture, structural engineering and mechanical, electrical and public health engineering. At this point you might be thinking 'two designers for architecture?' but imagine a project that brings together the best in each of their fields. That is the team we wanted to build.
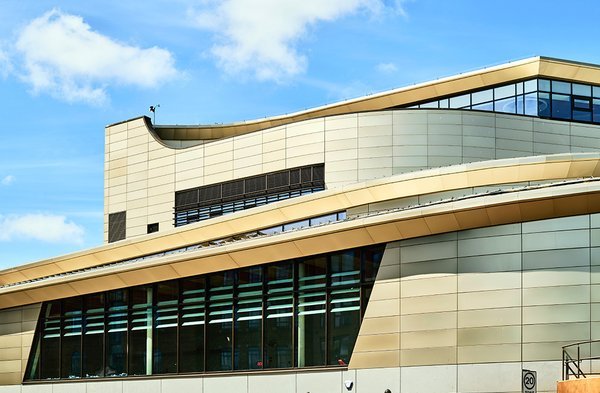
The sustainability outcomes were a bespoke set of environmental factors drawn from the TSB research into mitigating the impacts of future climate change and the Passivhaus Institute's (PHI) research into optimising low-energy passive design principles for swimming pool facilities.
The project brief for the facility included main and learner pools with moveable floors, changing village with fully equipped accessible changing rooms, a confidence water pool, a 100-spectator seating area, premium health spa, 150 station fitness gym, changing rooms, spin studio, café, crèche and soft play area.
A concept for swimming pools
Where the challenge was to achieve low in-use energy on a tightly constrained city centre site, the solution was to split the building into two interlinking forms, each accommodating 'wet' and 'dry' areas. Adjacent internal temperature zones are arranged to reduce energy losses between internal zones, and this is one of many passive design principles applied to reduce annual heating demand without increasing capital expenditure.
The total energy consumption of the building is an applaudable 375kWh/m2 per year. Other passive design principles included:
- Optimised envelope heat loss area
- Solar orientation of heated and cooled spaces
- Exceptionally airtight envelope
- Optimised thermal bridges at all junctions between assemblies
- Very high levels of insultation compared to standard buildings
- Heat recovery and reduced electrical energy demand for ventilation
Not to be mistaken for the 'classic' Passivhaus standard, the project uses the PHI's concept for swimming pool halls where higher humidity at pool level reduces latent heat loss from evaporation. The higher humidity levels are enabled by a high-performance building envelope, reducing the risk of internal surface condensation and mould growth, and in turn, allowing ventilation rates and energy losses to be reduced. At St Sidwell's Point, this new concept for swimming pools has been combined with the use of simultaneous heating and cooling air source heat pumps, meaning that the heat rejected from the cooling areas can be used to offset heat loads in the pool areas. These features are what makes the Passivhaus methodology a perfect fit for pool halls.
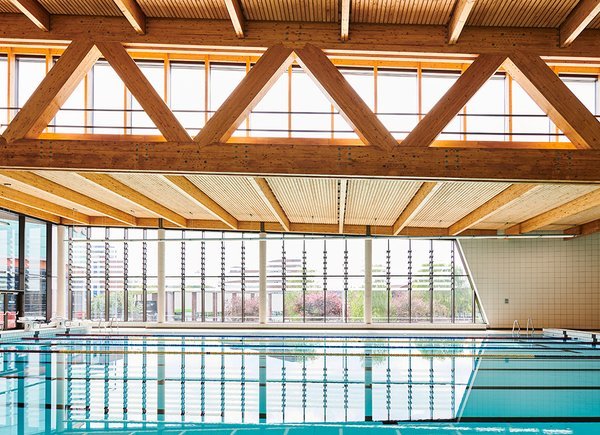
Energy is further reduced by using a microfiltration system. With microfiltration, pool water is forced through a semi-permeable ceramic membrane that filters the water to a finer grade than conventional sand filtration systems, removing unwanted particles and bacteria. Together, these measures result in one of the most sustainable leisure centres ever constructed. Along with 70% saving on energy costs, the scheme results in 50% reduction in water use, outstanding internal water quality, excellent daylighting levels, healthy internal environments, and reduced maintenance costs.
As if these features were not reason enough to dash to the shops for a new pair of speedos, the building has also been modelled to withstand predicted changes in climate conditions up to the year 2080. This means that the heated and cooled internal zones will be comfortable to use throughout the building's lifespan.
Developing a design
Through a series of design checks and re-assessments, the Passivhaus Institute modelled and defined the performance targets for the building using their own adapted set of Passivhaus Planning Package (PHPP) spreadsheets.
The certification process was specifically aimed at reducing the performance gap seen in buildings using standard methods of energy compliance in the UK. A post occupancy evaluation is being carried out to monitor the building during the first year of its operation, but the predicted energy demands are as follows:
- Space heating demand: 60 kWh/m2TFA/year
- Equivalent useful cooling demand: 22 kWh/m2TFA/year
- Pool water heating demand: 73 kWh/m2TFA/year
- Domestic hot water heating demand: 56 kWh/m2TFA/year
- Total electricity demand: 120 kWh/m2TFA/year
To achieve these targets, mechanical systems make use of greater than 80% efficiency heat recovery units, less than 5kWh/m2/year heating and DHW distribution losses, high coefficients of performance on heat pumps and greater than 90% gas boiler efficiency. Opaque envelope U-values are between 0.1 and o.14W/m2K, transparent element u-values are typically less than 1.2 W/m2K and psi-values are typically less than 0.01W/mK. Triple glazing with U-values of 0.59W/m2K are used throughout. The air permeability of the envelope has been verified at 0.3m3/hr/m2.
A marvel of Architectural Technology
During technical design stages, options were explored detail-by-detail to consider the implications of the project's environmental factors on buildability and sequencing. For example, the installation of the louvred panels needed to be airtight, weathertight, vapour-tight, and have good thermal continuity between the duct and the wall. Yet still, the assembly needed to be constructed internally and with limited working room. That particular detail was only resolved through a series of online and face-to-face design sessions between the contractor and design team.
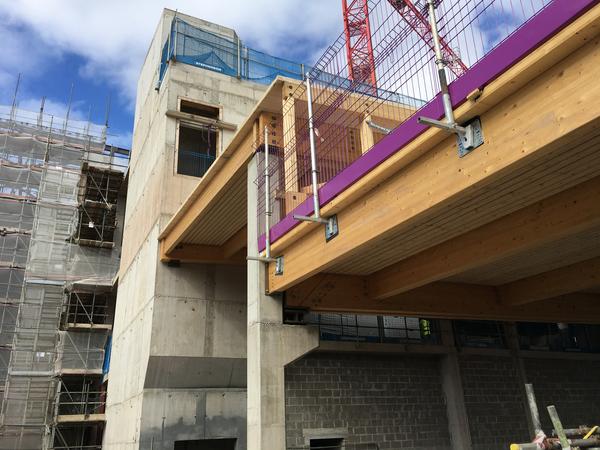
As you enter each of the two pool halls, you are greeted by the giant glue-laminated timber trussed beams spanning the length of each pool hall and supporting the cross-laminated timber roofs above. Mid-afternoon, full-height triple-glazed mullion-framed curtain walls allow light to pour through the south façade whilst also supporting the internal shading systems that reduce the amount of sunlight reflected from the pools surface. An in-situ concrete primary frame, substructure and shear walls provide a robust structure and convenient airtightness layer throughout much of the building envelope, and a composite sheathing board and fully-adhered vapour-permeable membrane allowed infill areas of external wall to be constructed without the impact of wet trades on the construction programme. The completed building is a marvel of Architectural Technology.
Constructing the team
No project is without its challenges, and no less this project than any other. On top of the usual design clashes, sequencing, safety, logistics and resourcing challenges, the contractors needed to deal with the COVID-19 pandemic and Brexit! At times, this meant labour shortages from workers travelling back to their home country, design changes due to product availability and transport delays. At one point our iconic glue-laminated beams were stuck on the other side of the English Channel!
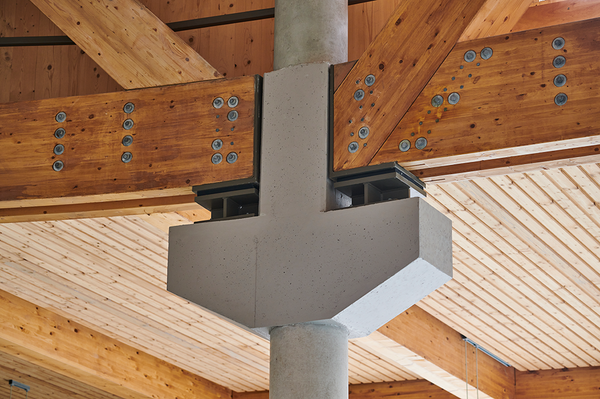
Despite all of this, contractors provided notable input to managing the risk of airtightness, including the construction of a series of on-site mock-up, phased and sectional air tests. Lessons were learnt from this process where large, super-airtight commercial buildings can be designed to make it easier to air test buildings without impacting the construction programme.
Insultation fixings were also a point of consideration where multiple layers of insulation resulted in significantly more fixings. The additional fixings had the potential to increase infiltration heat losses and transmission heat losses, the risk of which was managed through specific fixing details and technical submittals for every type of fixing in the façade.
The input and teamwork of the whole project team has resulted in a safe, healthy and environmentally sensitive facility available for use by the whole community. Exeter's new leisure centre makes a statement to local authorities throughout the UK that this level of investment in the health and wellbeing of the community is the way to bring communities closer togther and tackle physical inactivity.
Value of the contract
Construction cost: £35m
Project cost: £44m
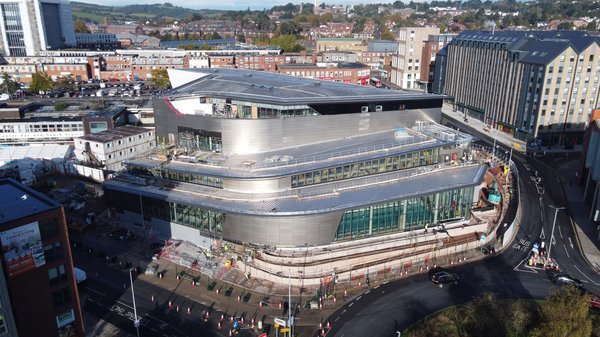
Watch Giles Boon FCIAT talks us through the design and construction stages of the first Passivhaus leisure centre in the UK